Mechanical parts textile steel collar deburring, descaling, polishing and brightening process technology method
How to deburr, descale, polishing and brightening the textile steel collars of mechanical parts?
Steel collars, also called spinning rings, are important textile machinery parts in spinning mills. They are made of high-quality carbon steel, alloy steel, bearing steel and other materials. Since the textile process has high requirements for the surface roughness of steel collars, the surface polishing process of the product is particularly important. In this case, we will share a process technology and method for deburring, descaling, and fine finishing and polishing of high-precision bearing steel collars. This polishing process solution is also suitable for the surface polishing of textile steel rings or other machined parts made of hard metal materials.
- jerrylu
- 2024-06-03
- 0 Comments
1. The textile steel collar before polishing
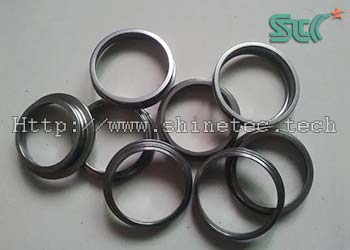
Materials:
bearing steel
Appearance:
edge burrs,surface oxide skin.
Shape:
circular ring
Size:
D46 MM
Pre-polishing process:
rolling
Post-polishing process:
packing
2. Finishing and polishing requirements
- descaling, derusting
- smooth, bright surface; no burrs, no oxide scale
3. Textile steel collar (spinning ring) polishing process details:
Process steps | (1) deburring,descaling of rough finishing | (2) fine polishing | (3) centrifugal drying |
---|---|---|---|
Machinery and equipment | centrifugal barrel finishing machine | centrifugal barrel finishing machine | centrifugal dryer |
Speed | highest | highest | highest |
Tumbling media | angle cut tri-star ceramic media | 3P polishing media | no |
Abrasive media to workpiece ratio | 4:1 | 6:1 | no |
Finishing and polishing compound | finishing liquid | polishing liquid | no |
Water | appropriate amount,the liquid level is 30mm above the abrasive media | appropriate amount,the liquid level is 30mm above the abrasive media | no |
Polishing time | 30 minutes | 30 minutes | 5 minutes |
Remark | parts separated and picked up automatically, rinsed with water | parts separated and picked up automatically, rinsed with water | centrifugal drying |
4. Textile steel collar (spinning ring) finishing and polishing effect
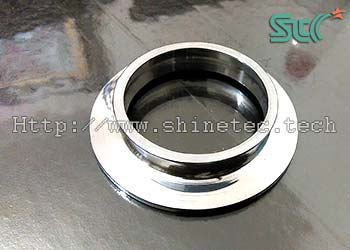
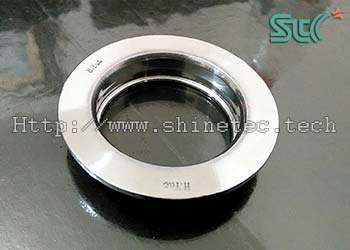
5. Additional instructions
-
The steel collar (spinning ring) is made of high-hardness bearing steel. The material hardness is very high, and the surface is required to meet the requirements of mirror polishing. Therefore, a polishing process solution combining rough finishing and fine polishing is adopted. The rough finishing adopts a centrifugal barrel finisher, and uses heavy cutting force angle cut tri-star tumbling media for rough deburring and descaling. The sharp angle of the tumbling media can reach into the grooves, corners, and inner walls to remove burrs and oxide layers.
Fine polishing still use centrifugal barrel polishing machines, and the ceramic media uses special precision finishing media 3P polishing media. This abrasive media has a high density and light cutting force. It can improve the surface brightness on the basis of precision cutting and achieve the effect of mirror polishing. - In order to improve the anti-rust and anti-corrosion performance of the product after water treatment, it is immersed in a anti-rust liquid for anti-rust treatment after polishing. Finally, a spin dryer is used to dry the surface moisture and dry it.
6. Final summary
- In this case study, we demonstrated the automated surface deburring, derusting, descaling and polishing process for a steel collar (spinning ring), a precision mechanical component used in the textile industry.
-
If you need professional technical support for the following textile machinery parts polishing issues, you can refer to the above cases:
Polishing process for precision textile machinery parts
Deburring process for precision textile machinery parts
Mirror polishing of textile steel collars
Polishing of cotton spinning steel collars
Polishing of fine yarn steel collars
Polishing of wire rings