How to remove burrs and oxide scales from hardware wrenches tools and achieve a mirror polishing surface?
Hardware wrench tool deburring,descaling and mirror polishing process technology method
Hardware tools are necessities in our daily production. The name of hardware originally refers to tools made of five metals: gold, silver, copper, iron, and tin. However, with the development of technology today, the materials used in hardware tools have long broken through the original five metal limitations and are changing with each passing day. Today we will share a case of deburring and descaling of an open-end wrench tool product made of chrome-vanadium alloy steel after stamping, reducing surface roughness, and mirror polishing. This finishing process solution is also suitable for the deburring, descaling, mirror finishing and polishing of hardware wrench tools made of other materials such as high-carbon steel, stainless steel, and high-manganese alloy steel.
- jerrylu
- 2024-06-08
- 0 Comments
1. Chrome vanadium alloy steel hardware wrench tool before polishing
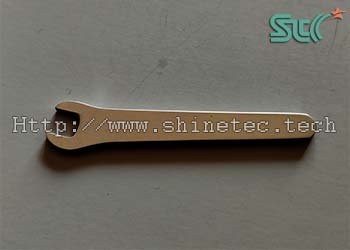
Materials:
chrome vanadium alloy steel
Appearance:
surface burrs, oxide scale.
Shape:
special-shaped
Size:
15*70 MM
Pre-polishing process:
standard stamping
Post-polishing process:
chrome plating
2. Finishing and polishing requirements:
- deburring, descaling
- surface mirror polishing
3. Chrome vanadium alloy steel hardware wrench tool polishing process details:
Process steps: | (1) deburring, descaling for rough finishing | (2) reduce roughness for fine finishing | (3) mirror polishing |
---|---|---|---|
Machine and equipment | centrifugal disc finishing machine | centrifugal disc finishing machine | mirror polishing machine |
Speed | highest | highest | highest |
Tumbling Media | angle cut tri-angle ceramic tumbling media | cone resin tumbling media | mirror polishing media |
Abrasive media to workpiece | 4:1 | 4:1 | 8:1 |
Chemical Compound | finishing compound | polishing compound | polishing paste |
Water | appropriate amount, liquid level does not exceed abrasive media | appropriate amount, liquid level does not exceed abrasive media | no |
Polishing time | 120 minutes | 60 minutes | 180 minutes |
Remark | parts separated and picked up automatically, rinsed with water | parts separated and picked up automatically, rinsed with water | high-speed mirror polishing |
4. Chrome vanadium alloy steel hardware wrench tool after polishing
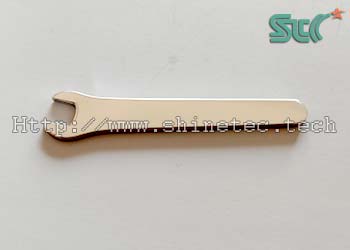
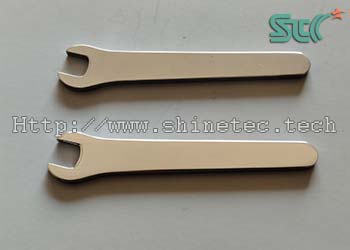
5. Additional instructions
- Chrome vanadium steel is an alloy tool steel with chromium (CR) and vanadium (V) alloy elements. Its comprehensive strength and toughness are better than carbon steel, making it an ideal material for high-quality tools. This product is small in size and requires high finishing efficiency. Therefore, the rough finishing machine uses a centrifugal disc finisher, which has strong finishing force and high cutting efficiency. The medium-cutting force of the angle cut tri-angle ceramic tumbling media is used for rough finishing, which can achieve the effect of rapid deburring and descaling.
- Fine finishing uses light cutting force plastic media, also called polyester media. This tumbling media has small grit size and light weight, will not cause deformation of the workpiece, and can further reduce the surface roughness.
- The last step after fine finishing is to use a mirror polisher and mirror polishing abrasive media to enhance the brightness and mirror polishing.
6. Final summary
- In this case study, we demonstrate the process of automated deburring, descaling, mirror finishing and polishing of the outer surface of a chrome-vanadium alloy steel hardware wrench tool.
-
If you need professional technical support for deburring, descaling, finishing and polishing of hardware wrenches tools made of stainless steel, high carbon steel, chrome-molybdenum steel, S2 tool steel, etc. or the following products, you can refer to the above cases:
Methods for deburring hardware tools
How to deburr hardware tools
Videos for deburring hardware tools
Videos for hardware tool polishing machines
Methods for polishing hardware tools
Hardware tool polishing machines
Polishing and finishing of wrenches
Differences between polished and not-polished of hardware wrenche tools
Methods for deburring hardware
Manufacturers of hardware deburring equipment
Hardware deburring machines
Deburring and polishing of hardware products
Hardware tool processing
How to finish and polish hardware