Mirror polishing technology of stainless steel dental probe for precision dental medical equipment parts
How to deburr, descale, and mirror-polish stainless steel dental probe parts for precision dental medical equipments?
The main materials used in the production of precision medical devices and parts are stainless steel, alloy steel, titanium alloy, nickel-titanium alloy and other metal materials. Due to their special uses, the surface must not have tiny pits, scratches and other defects, otherwise it will cause bacteria to grow and affect the patient’s life safety. Therefore, the mirror polishing process of the product surface is particularly important. In this case, we will share the process technology and method of automated and efficient deburring, descaling, brightening and mirror polishing of a stainless steel dental medical device part such as a dental probe. This finishing process solution is also applicable to the mirror polishing of precision medical equipment accessories made of other metal materials.
- jerrylu
- 2024-06-03
- 0 Comments
1. The dental probe of medical instrument before polishing
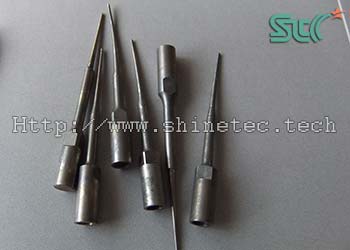
Materials:
stainless steel
Appearance:
burrs and oxide layer on surface
Shape:
sharp needle
Size:
D4*45 MM
Pre-polishing process:
annealing
Post-polishing process:
packing
2. Finishing and polishing requirements
- deburring, descaling.
- smooth surface, no burrs, oxide scale, mirror polishing.
3. Details of the mirror polishing process for dental probe:
Process steps | (1) deburring,descaling of rough finishing | (2) brightening of fine finishing | (3) mirror polishing |
---|---|---|---|
Machinery equipment | centrifugal barrel finishing machine | centrifugal barrel finishing machine | centrifugal barrel finishing machine |
Speed | highest | highest | highest |
Tumbling media | angle cut cylinder ceramic media | straight cut cylinder high-density porcelain media | walnut shell mirror polishing media |
Abrasive media to workpiece ratio | 4:1 | 6:1 | 8:1 |
Finishing and polishing compound | finishing liquid | polishing liquid | mirror polish paste |
Water | appropriate amount,the liquid level is 30mm above the abrasive media | appropriate amount,the liquid level is 30mm above the abrasive media | no |
Polishing time | 60 minutes | 30 minutes | 60 minutes |
Remark | parts separated and picked up automatically, rinsed with water | parts separated and picked up automatically, rinsed with water | mirror polishing effect |
4. Mirror polishing effect of stainless steel dental probe of medical instruments
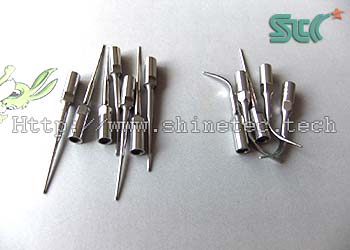
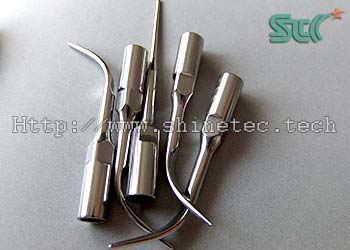
5. Additional instructions
-
The dental probe is made of stainless steel. After annealing, there is a thick oxide layer on the surface of the product, the color is black, and there will be slight burrs on the edge of the hole. It is necessary to remove the burrs, oxide scale, reduce the surface roughness, and further improve the brightness. Therefore, the finishing process combining rough deburring, descaling and fine finishing and mirror polishing is adopted. The polishing machine uses centrifugal barrel finisher with heavy cutting force angle cut cylinder ceramic tumbling media. The sharp angle of the ceramic deburring media can reach into the grooves, corners, and inner walls to achieve the effect of removing burrs and oxide layers.
Fine finishing uses precision polishing media without cutting force straight cut cylinder high-density porcelain polishing media, which has a high density and has a polishing and brightening effect, which can further reduce the surface roughness.
In order to improve the anti-rust performance of the product after water treatment, after fine finishing, use a centrifugal spin dryer to dehydrate and dry the moisture on the inner and outer product surfaces. - For mirror polishing, use walnut shell mirror polishing media and polishing paste to achieve a mirror-like surface effect.
6. Final summary
- In this case study, we demonstrated the process of automated surface deburring and descaling of stainless steel probe used in the dental medical industry to achieve mirror polishing.
-
If you need professional technical support for mirror polishing of stainless steel, alloy steel, titanium alloy, nickel-titanium alloy and other medical equipment accessories or other precision medical equipment parts, you can refer to the above cases:
Polishing of precision medical equipment
Polishing of precision medical equipment accessories
Mirror polishing of medical equipment
How to polish dental medical equipment accessories
Mirror polishing of dental equipment parts
Deburring and polishing of medical surgical instruments (such as scalpels, hemostats, scissors and other tools);
Artificial prostheses (such as mirror polishing of knee joints, etc.)
Polishing of oral equipment (such as dentures, dental trays, dental correction equipment, etc.)
Deburring and polishing of heart bypass stents
Deburring and polishing of inner and outer walls of stainless steel needle tubes/needles
Polishing of titanium alloy bone nails
Polishing of dental steel trays
Polishing methods of dental devices
Polishing methods of dental metal finishing and polishing methods