How to deburr, descale, polish carbide mechanical seal parts?
Finishing and polishing technology of mechanical seal parts of cemented carbide products
Mechanical seals are precise and complex basic mechanical components. Commonly used metal materials include hard alloys (such as tungsten carbide), high silicon iron, nickel-chromium steel, chrome steel, bronze, carbon steel and cast iron, etc., which will produce burrs, flash, scratches, oxide scale and other defects during the manufacturing process. Do you know what kind of finishing and polishing process mechanical seal parts need to go through to obtain a satisfactory surface effect? In this case, we will share the process technology and methods of deburring, derusting, descaling, polishing and brightening of a hard alloy mechanical seal product. This polishing process solution is also suitable for the surface polishing of sealing parts made by other hard metal materials.
- jerrylu
- 2024-06-03
- 0 Comments
1. Cemented carbide mechanical seal before polishing
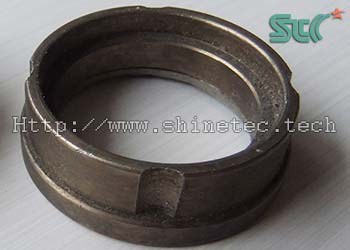
Materials:
tungsten carbide
Appearance:
edge burrs, surface oxide scale
Shape:
circular
Size:
D 50MM
Pre-polishing process:
powder metallurgy
Post-polishing process:
product assembly
2. Finishing and polishing requirements
- chamfer and remove flash, grooves without burrs.
- smooth, bright surface, no burrs, no oxide scale.
3. Details of carbide mechanical seal polishing process:
Process steps | (1) rough finishing of chamfering, deburring, descaling | (2) fine polishing | (3) anti-rust drying |
---|---|---|---|
Machinery and equipment | centrifugal disc finishing machine | centrifugal barrel finishing machine | vibratory dryer |
Speed | highest | highest | highest |
Tumbling media | straight cut tri-angle ceramic media | 3P finishing media | corn cob drying media |
Abrasive media to workpiece ratio | 4:1 | 6:1 | 8:1 |
Finishing and polishing compound | finishing liquid | polishing liquid | no |
Water | appropriate amount, liquid level is 20mm above the tumbling media | appropriate amount, liquid level is 20mm above the tumbling media | no |
Polishing time | 30 minutes | 30 minutes | 15 minutes |
Remark | parts separated and picked up automatically, rinsed with water | parts separated and picked up automatically, rinsed with water | vibratory drying |
4. Finishing and polishing effect of cemented carbide mechanical seal
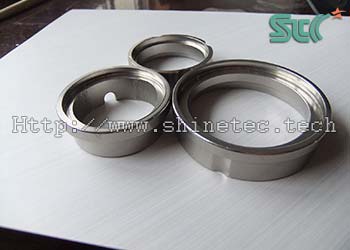
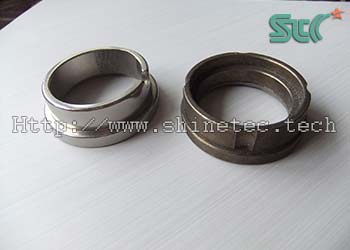
5. Additional instructions
-
The hardness of tungsten carbide is generally between HRA87 and 94. The product volume is not large, so a centrifugal disc finisher is used, with heavy cutting force straight cut tri-angle ceramic media for rough finishing. The sharp tip of the tumbling media can reach into the groove to remove burrs and chamfers.
Fine polishing uses a centrifugal barrel finisher with high centrifugal force, so the tumbling media uses high-hardness 3P fine polishing media, which can cut lightly, further reduce the roughness and improve the surface brightness. - In order to improve the anti-rust and anti-corrosion performance of the product after water treatment, it is immersed in a anti-rust liquid for anti-rust treatment after polishing. Finally, a a href=”http://www.shinetec.tech/index.php/en/product/vibratory-dryer-vibrating-drying-machine/” target=”_blank” rel=”noopener”>vibrating dryer is used to dry the surface moisture and dry it.
6. Final summary
- In this case study, we demonstrate the process of chamfering, deburring, descaling, polishing and brightening the surface of a mechanical seal part made of tungsten carbide.
-
If you need professional technical support for the following mechanical seal product polishing issues, you can refer to the above cases:
Mechanical seal polishing process technology
Mechanical seal deburring process technology
Mechanical parts polishing process technology
Mechanical parts deburring process technology
Metal parts polishing
What abrasive is suitable for carbide polishing
Introduction to carbide polishing technology
Carbide deburring polishing process
How to polish carbide
What to use for polishing carbide
Methods for descaling of carbide
Cemented carbide surface polishing
What finishing and polishing materials are used for carbide
Mirror polishing of carbide