Deburring,descaling and polishing method of copper alloy die castings (floor sockets)
How to chamfer, deburr, descale, polish and brighten copper alloy die castings?
Copper alloy die casting is a mature and versatile production process, which is used to manufacture a variety of hardware parts products. Commonly copper alloys include copper-aluminum alloy, copper-zinc alloy, copper-nickel alloy, etc. Die casting products will produce burrs, flash, scratches, oxide scale and other defects during the production process. Do you know what kind of finishing and polishing process copper alloy die castings need to go through to obtain a satisfactory surface effect? In this case, we will share a copper alloy floor socket deburring, descaling, polishing, brightening process technology and methods. This polishing process solution is also suitable for the surface polishing of brass, zinc alloy, aluminum alloy, magnesium alloy and other products.
- jerrylu
- 2024-06-03
- 0 Comments
1. copper alloy floor outlet before polishing
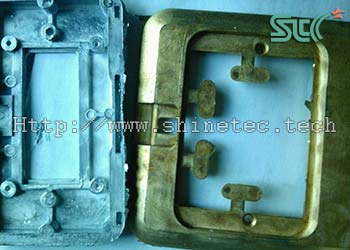
Materials:
copper-zinc alloy
Appearance:
burrs on the edges,oxide scale on the surface
Shape:
square
Size:
120*120MM
Pre-polishing process:
die casting
Post-polishing process:
electroplating
2. requirements for polishing
- chamfer and remove flash, grooves without burrs.
- smooth and bright surface, no burrs, no oxide scale
3. Copper alloy floor outlets polishing process details:
Process steps | (1) rough finishing, chamfering, deburring, descaling | (2) fine polishing | (3) vibratory drying |
---|---|---|---|
Machine and equipment | vibratory finishing machine | vibratory finishing machine | vibratory dryer |
Amplitude and speed | highest speed | highest speed | highest speed |
Tumbling media | Cone resin media | Spherical white corundum finishing media | corn cob polishing media |
Abrasive media to workpiece ratio | 4:1 | 6:1 | 8:1 |
Finishing and polishing compound | finishing liquid | polishing liquid | no |
Water | appropriate amount, the liquid level does not exceed the tumbling media | appropriate amount, the liquid level does not exceed the tumbling media | no |
Polishing time | 60 minutes | 30 minutes | 15 minutes |
Remark | parts separated and picked up automatically, rinsed with water | parts separated and picked up automatically, rinsed with water | vibrating drying |
4. copper alloy floor outlet after finishing and polishing
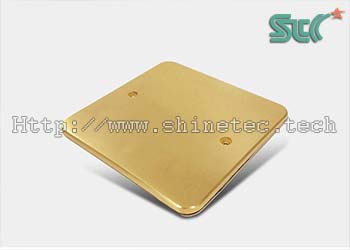
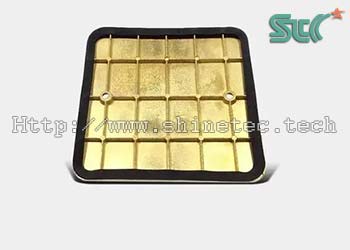
5. Additional instructions
-
Copper alloy floor outlets have low hardness and are medium-sized product parts with a large daily processing quantity. Therefore, a vibratory polishing machine is used with a cone plastic media with low hardness to perform rough finishing. The conical tip can touch deep into the groove to remove burrs and chamfers.
Fine polishing and brightening is also achieved by using a vibrating finishing machine, with spherical white corundum finishing media with high hardness and light cutting force, which can cut a small amount, further reduce the roughness and improve the surface brightness. - In order to improve the anti-rust and anti-corrosion performance of the product after water treatment, it is immersed in the anti-rust liquid for anti-rust treatment after polishing. Finally, a vibrating dryer is used to dry the surface moisture and dry it.
6. Final summary
- In this case study, we demonstrate the process of chamfering, deburring, descaling and polishing the surface of a copper alloy die-casting component, a floor socket.
-
If you need professional technical support for the following product polishing issues, you can refer to the above cases:
Die casting surface treatment process
Die casting polishing process
Die casting deburring process
Die casting deburring method
How to remove oxide scale from die casting
Descaling of die casting aluminum
Copper alloy die casting product polishing process
Copper alloy hardware polishing
Copper alloy mechanical polishing
Copper alloy polishing skills
Copper alloy die casting deburring method
How to deal with copper alloy die casting deburring
Copper alloy deoxidation method
Aluminum alloy die casting product polishing process
Zinc alloy die casting product polishing
Aluminum alloy die casting product deburring
Aluminum alloy hardware polishing
How to deburr zinc alloy hardware