What can we do
ShineTec is an industry-leading company that provides surface finishing and polishing solutions for mechanical parts and product workpieces. We have many years of surface treatment experience serving many industrial fields, including:
Mechanical accessories, plastic products, auto parts, 3C digital, metal casting, electronic devices, medical equipment, hardware parts, kitchen supplies, aerospace, 3D printing, textile workpieces, powder metallurgy, electrical components, mint industry, jewelry, instruments Instruments, handicraft accessories and other industries.
For manufacturers in many different industrial fields around the world, ShineTec is your reliable supplier with guaranteed quality. We will provide you with high-quality product finishing, polishing and brightening processes. If you choose us during production and processing, you should be confident that you are processing your products with the most reasonable cost and the best process solution, and you will enjoy reliable service and support. At the same time, we are proud of our many years of surface treatment technology and experience, ranging from small watch parts to large aerospace engine parts.
Deburring, Deflashing
During the manufacturing process, metal or non-metal parts will undergo a series of processing techniques, such as grinding, drilling, milling, turning, tapping, grooving, etc. It is inevitable that excess protrusions will be left after processing. Or thorn-like objects, which are what we usually call burrs. Although burrs are small, they directly affect the appearance and use of the product, and even cause safety problems, so burrs must be removed.
Especially for product parts with special shapes and complex cavities, a large number of burrs and flash will be generated on both the inner and outer surfaces during cutting, stamping, casting, forging, electric welding, etc. So how can we achieve fast and efficient Automatic Deburring And Deflashing? Choosing the right equipment and techniques for finishing will get twice the result with half the effort.
Unlike manual grinding using files, sandpaper, polishing heads and other tools, our finishing and polishing equipment and abrasive media can meet your requirements through automatic mechanization, large quantities, low cost and high efficiency. It is suitable for all types of irregular-shaped parts, especially some cross-section parts. Holes, pipe inner walls, dead corners, cracks and other parts that are not easily reached by manual polishing tools can be ground and processed.
Products have different shapes, materials, specifications and sizes. We will provide mature and reliable solutions based on samples. In the field of surface treatment, we are worthy of your trust.
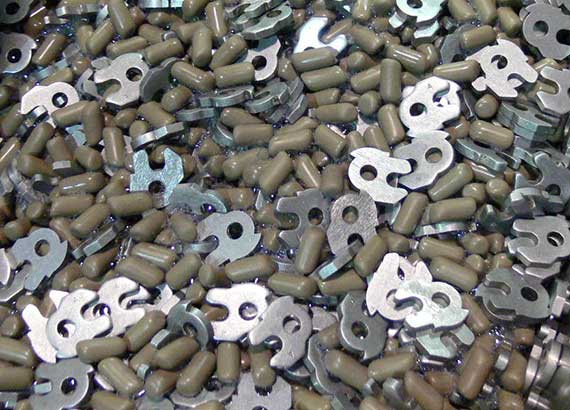
Descaling
Oxidation of the metal surface over time will corrode the metal surface and shorten its service life. Metal materials such as steel, aluminum, copper, etc., if exposed to the air for too long or after heat treatment, the surface will definitely produce oxidation phenomena such as rust, skin explosion, delamination, corrosion, etc. Commonly used rust removal methods include pickling, shot blasting and other processes.
As we all know, pickling is a treatment method that is harmful to the natural environment. It is not environmentally friendly, highly toxic, and prone to excessive corrosion. Shot blasting and sandblasting are not suitable for some products with complex shapes or internal holes and gaps.
Our vibratory, centrifugal barrel, disc, and barrel type finishing and polishing processes can remove rust and scale in an environmentally friendly, safe, low-cost, high-efficiency, mechanized way, and better solve the problem of rust and oxidation on the product surface, improve the surface quality and return the original appearance of your product parts.
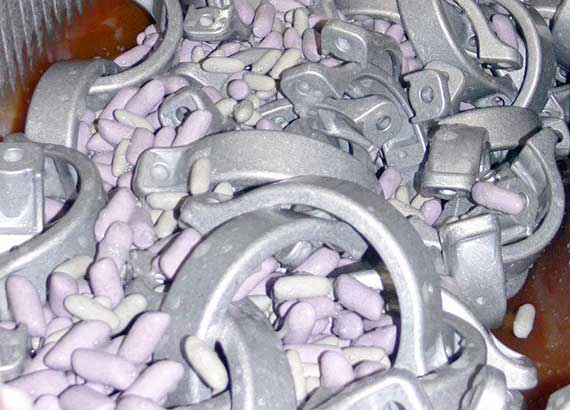
Chamfering and Molding Line Removing
Non-standard CNC processing parts, laser cutting parts, stamping parts, sheet metal parts, powder metallurgy workpieces such as NdFeB, metal casting, 3D printing and other products are prone to burrs or flash due to machining. The purpose of chamfering is Remove these flash burrs so that the edges of the product are not sharp and will not cut the user.
There will be a mold closing line left on the surface of the finished injection molded part, which also needs to be removed to create a smooth and rounded surface effect.
After the parts are chamfered, the parts are neat and beautiful, with no sharp edges, which protects the transportation and facilitates assembly.
After the chamfered metal material is heat treated, it is beneficial to the release of stress. The chamfered workpiece is not prone to cracks, which can reduce deformation and solve the problem of stress concentration.
After the machining process of machined parts is completed, the surface is prone to defects such as turning marks, chips, and cracks. The deburring and finishing process can remove these surface defects while chamfering, improve product surface quality, reduce material loss, increase yield, and reduce production costs.
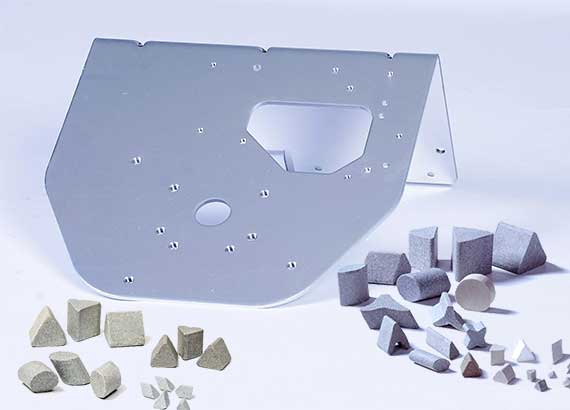
Degreasing and Cleaning
Are you worried because the finished parts are stained with various oil stains and sludge, resulting in incomplete cleaning in subsequent processes?
Oil stains on machined parts are mainly formed by unsaponifiable oil, dust, impurities, etc. These oils are not soluble in water and do not react with strong alkalis. For large batches of small and medium-sized machined parts, manual cleaning is too inefficient. Organic solvents or chemical cleaning solutions also need to be prepared. Moreover, most of these solvents are flammable, high in cost, and low in safety. Some parts with serious oil stains on the surface require additional auxiliary processes such as boiling and spray cleaning, making the process shortcomings more obvious.
Another method in the industry is to use ultrasonic cleaning. It uses the cleaning liquid and the workpiece to remove oil stains under the action of ultrasonic oscillation. However, its disadvantage is that it is not suitable for large-volume processing needs. Because ultrasonic machines are generally miniaturized.
The vibrating cleaning process we provide is to put finishing compound liquid or cleaning liquid, tumbling ceramic media and large quantities of workpieces into a vibratory finishing machine for cleaning. The finishing liquid itself undergoes a chemical reaction and participates in roller-throwing grinding together with the abrasive to remove oil stains on the surface. The three materials are rolled and tumbling in the machine, simulating manual rinsing action, and the oil stains are efficiently removed under the chemical action of finishing compound and cleaning liquid.
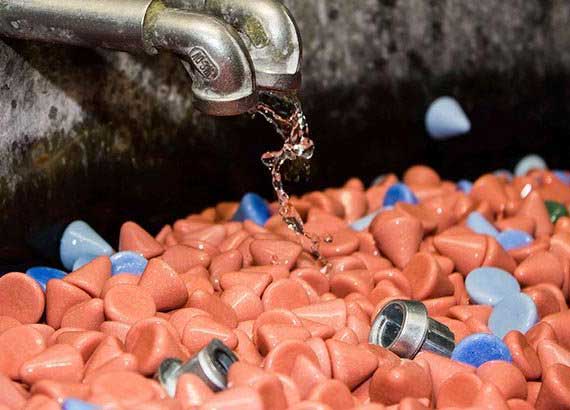
Brightening and Burnishing
For some stainless steel, brass, copper, aluminum-magnesium alloy, handicrafts, jewelry and other parts and components, or precision machined parts, improving the gloss and brightness of the product surface is a process requirement with huge market demand.
Our tumbling mass finishing and polishing process uses high-density tumbling media, such as high-alumina porcelain media, high-density porcelain polishing media, stainless steel media, and white corundum polishing media, based on the rough finishing in the previous process. Tumbling media and other materials, with the cooperation of brightening chemical polishing liquid, produce high-frequency precision finishing, micro-cutting and impact effects in the finishing machine. Under the grinding action of the abrasives, on the one hand, they produce cutting effects and reduce the surface roughness of the product. On the other hand, it improves the dense layer on the surface of the product to achieve the purpose of improving surface brightness and gloss.
Whether it is a standard part with a regular shape or a non-standard product with a special shape and complex cavity, we can give you a dazzling internal and external surface effect.
